Construção mercado 89 - dezembro 2008
Nos últimos dois anos, o Grupo Capuche, formado pelas incorporadoras e construtoras Capuche, Viverde e Ecomax, dobrou de produção: saltou de 156.667 m2 em 2007 para 315.750 m2 em 2008. No próximo ano, o volume construído alcançará a ordem de 610.965 m2. Para promover esse salto o grupo modificou radicalmente seus processos de gestão e adotou a filosofia de negócios baseada no Sistema Toyota de Produção, mais conhecida como lean construction. Em geral, o modelo analisa com detalhe as atividades básicas envolvidas no negócio e identifica o que é desperdício e o que é valor a partir da ótica dos clientes e usuários, propondo soluções de melhoria.
Foi exatamente no início da implementação desse processo que a construção do Residencial Caminho do Sol, na área mais nobre de Capim Macio, em Natal, empreendeu mais de 10 mil m2 de área construída. O projeto foi o primeiro do grupo a aplicar os conceitos de construção enxuta, que visa reduzir custos de estoque, otimizar os recursos e eliminar desperdícios de qualquer ordem. O sucesso da iniciativa - 18% de aumento na produtividade, o que representou economia de 3,18% no orçamento global da obra - foi fundamental para a adoção do modelo em todas as obras da empresa.
Mas antes de chegar a esse resultado, o primeiro passo, segundo Fernando Arraes, diretor técnico do Grupo, foi mapear o que chama de "DNA da Capuche", identificando os indicadores, os fluxos e a logística da empresa para, a partir deles, criar um sistema de gestão próprio - que, por lá, foi chamado de Simples.
Nessa etapa, os gestores identificaram que havia um tempo ocioso entre as tarefas da obra. Contra isso, a construtora agrupou os serviços da empreitada em 37 pacotes de produção, sendo 18 executados diretamente pelos funcionários da empresa e 19, por terceiros. O pacote 1, por exemplo, previa marcação da alvenaria; colocação de tela ancofix; chapisco estrutural, estudo das alturas do piso para definição das alturas de porta, entre outros. No pacote 2: execução da alvenaria interna; emestramento de piso de áreas secas; colocação de vergas e contravergas internas, e assim por diante.
Com isso, as equipes passaram a ser multifuncionais e não mais especializadas. "Quando fazia o reboco, o trabalhador não precisava mais esperar a argamassa secar para depois vir com a régua cortando para dar acabamento. Enquanto ele esperava a argamassa, ele fazia outra coisa, porque participava de todo pacote e não de uma função", explica Arraes.
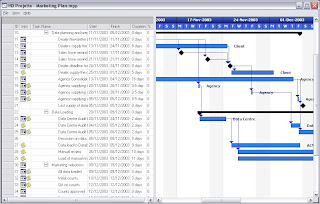
PRODUÇÃO PUXADA
A criação de células de trabalho foi o ponto de partida para o início da transformação do canteiro, onde a execução passou a ser iniciada pela última etapa do processo, ou seja, o operário. Seguindo o modelo de produção "puxada" - e não "empurrada" - a responsabilidade da solicitação de produtos e de materiais para execução dos serviços ficou por conta dos trabalhadores da obra, e não mais das lideranças. O modelo é pautado no sistema kanban, em que não se produz nada até que o cliente (interno ou externo) de cada processo solicite a produção de determinado item por meio de quadros de aviso e de nivelamento da produção, ferramenta utilizada para nivelar o mix e o volume produzido distribuindo os avisos em uma instalação em intervalos fixos.
Assim, as turmas solicitam o necessário para cada dia, tornando o estoque no pavimento o menor possível. Da mesma maneira, o transporte de materiais é feito conforme os pedidos, permitindo uma entrega ordenada. "Com o quadro e o cartão de sinalização, o pedreiro diz o que ele quer, a hora que ele quer e em que quantidade, ou seja, quero tantos tijolos no pavimento tal, às dez horas. Daí, uma equipe vai se mobilizar para deixar o material exato lá", conta Arraes.
Além disso, cada pacote foi planejado em períodos diferentes e por grupos hierárquicos distintos. No longo prazo, foram os gerentes e diretores da empresa que traçaram o plano mestre da obra. Já no médio, 90 dias, a responsabilidade era dos gestores das obras. E no curto prazo (semanal), o planejamento era administrado pelos próprios operários. Com isso, a empresa computou a quantidade média de materiais utilizados em um dia; o tempo de duração do serviço e valores de mão-de-obra; a qualidade de cada serviço; a freqüência de solicitação de materiais, embalagem, local de uso e armazenagem, logística de abastecimento, e o número de sinais de puxada (embalagens vazias, kanban etc.).
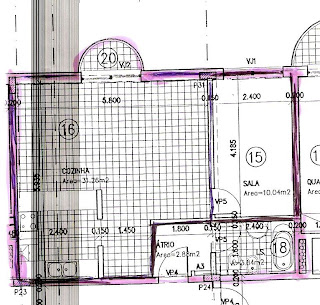
E como quem compila dados, mensura resultados, Fernando Arraes diz que o método tem trazido um melhor controle orçamentário, já que a empresa passou a controlar na fonte o consumo de materiais e o custo da mão-de-obra (por meio dos kanbans - avisos); maior estabilidade da produção, mantendo um nível baixo dos estoques e uma redução significativa nos produtos fora do padrão. No quesito redução de desperdícios, as variáveis são inúmeras: redução do tempo de espera para execução de serviços; diminuição do retrabalho; abatimento dos níveis de estoque por meio da produção de pequenos lotes e do nivelamento da produção e redução significativa nos transportes vertical e horizontal e na movimentação.
Fonte: Revista Construção Mercado N. 89 / Dez. 2008
Nenhum comentário:
Postar um comentário